Vinyl plank flooring is made by combining polyvinyl chloride (PVC) with additives for durability and flexibility. The materials undergo a heating process, forming a molten compound, which is then extruded into sheets. Advanced printing technology imparts realistic wood designs onto these sheets. After cooling, the sheets are cut and shaped into planks. Stringent quality control measures, including testing for impact and moisture resistance, guarantee high standards. Discover more about its layer composition and innovative production methods.
Overview of Vinyl Plank Flooring
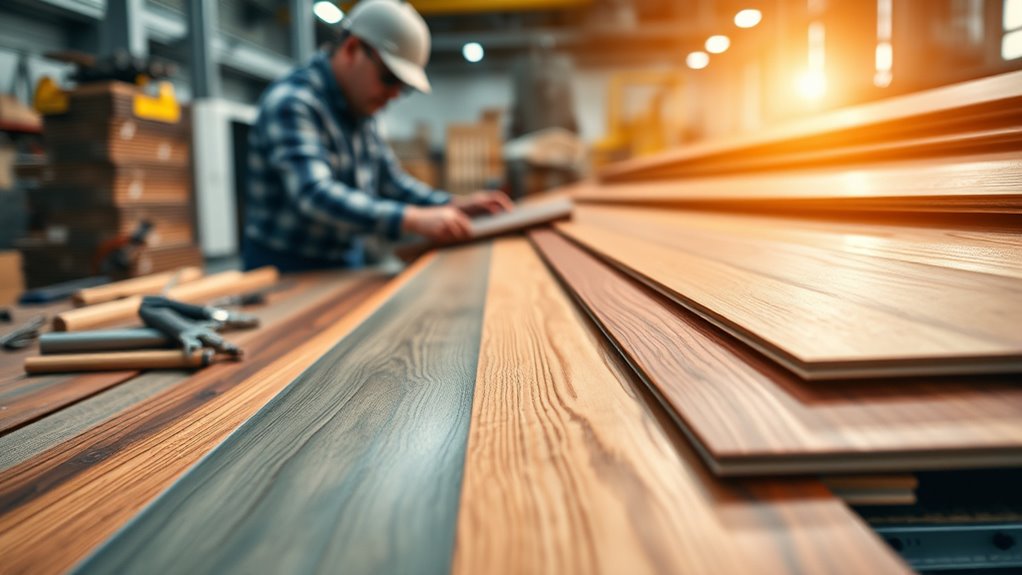
Vinyl plank flooring, while often mistaken for traditional hardwood, offers a unique blend of durability and aesthetic appeal that makes it a popular choice for many homeowners. This flooring option provides a thorough benefits overview, showcasing resistance to moisture, scratches, and stains. With a variety of designs mimicking natural wood, it caters to diverse tastes while ensuring ease of maintenance. Recent market trends indicate a significant shift towards eco-friendly materials and manufacturing processes, reflecting a growing consumer preference for sustainability. As you explore vinyl plank options, consider how these advancements align with your desire for freedom in home design, providing both style and practicality without compromising on quality or environmental responsibility.
Raw Materials Used in Production
In the production of vinyl plank flooring, the primary raw material is polyvinyl chloride (PVC), which forms the backbone of the product's structure. You'll also find various additives and fillers that enhance properties like durability, flexibility, and resistance to wear. Understanding these components is essential for evaluating the overall quality and performance of the flooring.
Polyvinyl Chloride (PVC)
Polyvinyl chloride (PVC) serves as the cornerstone of vinyl plank flooring production, providing durability and versatility. Its properties, such as resistance to moisture, impact, and abrasion, make it an ideal choice for high-traffic areas. You'll find that PVC applications extend beyond flooring; it's also used in pipes, medical equipment, and insulation, showcasing its adaptability across various industries. The molecular structure of PVC allows for modification, enhancing its performance characteristics tailored to specific needs. As you explore vinyl plank flooring, understanding PVC's role helps you appreciate its long-lasting nature and ease of maintenance. This foundational material contributes considerably to the overall quality and functionality that vinyl plank flooring offers in residential and commercial settings.
Additives and Fillers
To enhance the performance and functionality of PVC in vinyl plank flooring, various additives and fillers are incorporated during production. These components play vital roles in optimizing the material's characteristics and durability.
Here are three key additive types and their filler purposes:
- Plasticizers – These improve flexibility, making the flooring more comfortable underfoot.
- Stabilizers – They prevent degradation from heat and UV exposure, ensuring longevity.
- Colorants – Used for aesthetic appeal, they allow for a wide range of design options.
The Manufacturing Process: Step-by-Step
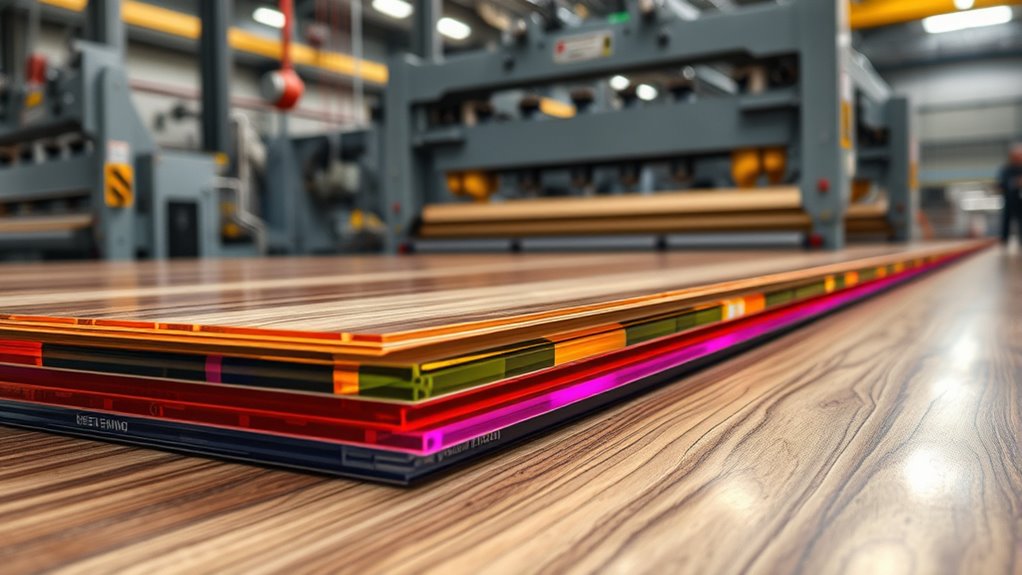
While understanding the manufacturing process of vinyl plank flooring may seem intimidating, it actually involves a series of well-defined steps that guarantee high-quality production. First, raw materials, including PVC resins and additives, are sourced with an eye on sustainability practices. These materials are then blended and heated to create a molten compound. Next, this mixture is cooled and extruded into sheets. Advanced technology allows manufacturers to imprint realistic designs, aligning with current market trends. Following this, the sheets undergo a calendering process to achieve the desired thickness and texture. Finally, the sheets are cut into planks and inspected for quality control. Each step is essential for delivering a product that meets your expectations for durability and aesthetic appeal.
Layer Composition of Vinyl Plank Flooring
When considering vinyl plank flooring, the layer composition plays an essential role in its performance and durability. The core layer materials, typically made from PVC or other composites, provide stability and moisture resistance, while the surface wear layer protects against scratches and stains. Understanding these components helps you evaluate the flooring's suitability for your environment.
Core Layer Materials
The core layer of vinyl plank flooring plays a crucial role in its overall durability and performance. This layer provides structural integrity and enhances various durability factors. Understanding the materials used can help you make informed choices. Here are three common core layer materials:
- PVC (Polyvinyl Chloride): Known for its water resistance and flexibility, PVC is a reliable choice for high-moisture areas.
- WPC (Wood Plastic Composite): Combining wood fibers and plastic, WPC offers enhanced comfort and warmth underfoot.
- SPC (Stone Plastic Composite): With a rigid core, SPC provides superior durability and impact resistance, ideal for high-traffic spaces.
Choosing the right core layer guarantees your flooring withstands the test of time while offering the freedom to enjoy your space.
Surface Wear Layer
Following the core layer, the surface wear layer is essential for protecting vinyl plank flooring from daily wear and tear. This layer typically consists of a transparent urethane coating that enhances surface durability, making it resistant to scratches, stains, and scuffs. The thickness of this layer can vary, influencing both performance and longevity. A thicker wear layer often translates to lower maintenance requirements, allowing you to enjoy your flooring without constant upkeep. When considering options, assess the wear layer's specifications to guarantee it meets your lifestyle needs. Ultimately, a robust surface wear layer not only safeguards your investment but also contributes to the overall aesthetic, ensuring your flooring remains beautiful and functional over time.
Printing Technology for Realistic Designs
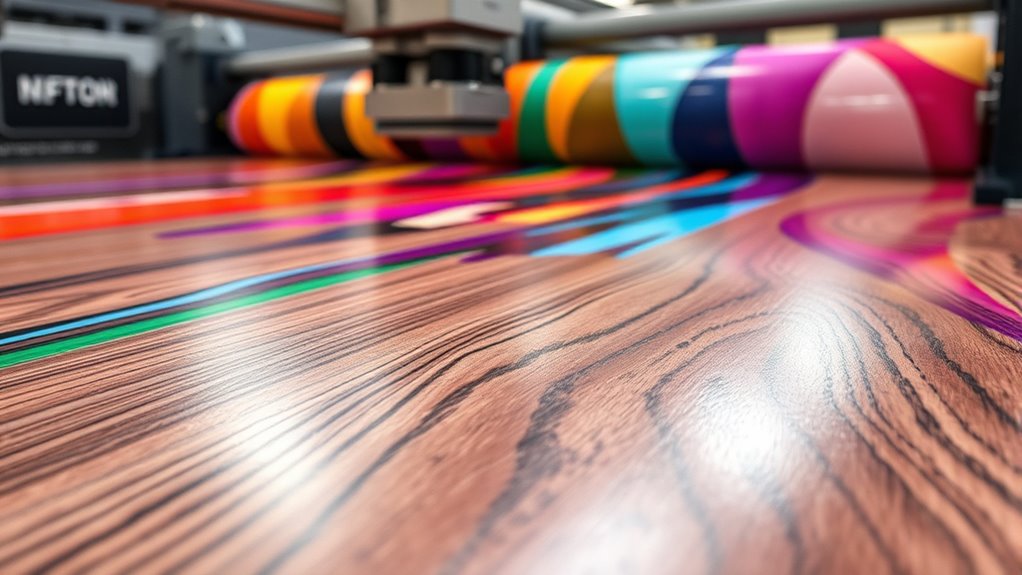
As manufacturers endeavor to create visually appealing vinyl plank flooring, advanced printing technology plays an essential role in producing realistic designs that mimic natural materials. Digital printing techniques allow for remarkable design accuracy, ensuring that every plank captures the essence of wood, stone, or tile.
Imagine the following elements brought to life:
- Grain Patterns: Intricate textures that resemble aged oak or rich mahogany.
- Color Variations: Subtle shifts in hue that echo the natural imperfections found in real wood.
- Surface Details: Enhanced depth and shading that create a three-dimensional feel.
These innovations not only create stunning visuals but also provide the freedom to choose from an array of styles that suit any aesthetic preference, transforming spaces effortlessly.
Cutting and Shaping the Planks
While precision is essential in the production of vinyl plank flooring, cutting and shaping the planks involves advanced machinery that guarantees uniformity and accuracy. Various cutting techniques, such as laser and CNC cutting, assure that each plank meets specific dimensions with minimal waste. These methods allow for intricate designs and precise edges, enhancing the overall aesthetic appeal. After cutting, shaping methods come into play, where the planks are contoured to achieve the desired thickness and profile. This process often includes beveling and rounding edges, facilitating easier installation and a seamless look. By integrating these cutting and shaping technologies, manufacturers provide you with high-quality flooring that not only looks great but also fits perfectly within your space.
Quality Control and Testing
Before vinyl plank flooring reaches your home, it undergoes rigorous quality control and testing to guarantee durability and performance. This process guarantees that each plank meets high standards through established testing protocols and quality assurance measures. Key areas of focus include:
- Impact Resistance: Testing how well the planks withstand heavy objects without damage.
- Moisture Resistance: Evaluating the planks' ability to resist water exposure, vital for longevity.
- Colorfastness: Confirming that the color of the vinyl remains vibrant over time, even under UV exposure.
Installation Methods and Options
When considering the installation of vinyl plank flooring, you'll find several methods and options that cater to different preferences and environments. The most common installation techniques include glue-down, click-lock, and loose lay. Each method presents unique advantages; for instance, click-lock systems are user-friendly and ideal for DIY enthusiasts, while glue-down is preferred for high-traffic areas due to its durability. However, installation challenges can arise, such as ensuring a level subfloor and managing temperature fluctuations. It's essential to assess your space's conditions and your skill level before deciding on an installation method. By understanding these options, you can achieve a seamless and aesthetically pleasing floor that meets your needs without compromising your freedom to customize your living space.
Environmental Considerations in Vinyl Production
As you explore vinyl plank flooring, it's important to contemplate the environmental impact of its production. Manufacturers are increasingly adopting sustainability practices to mitigate potential harm. Consider these aspects:
- Raw Material Sourcing: Many companies seek to use responsibly sourced materials, minimizing ecological damage.
- Energy Efficiency: Modern production facilities often implement energy-efficient technologies to reduce carbon footprints.
- Recycling Initiatives: Some brands actively engage in recycling initiatives, reclaiming old vinyl to create new products, which reduces waste.
These considerations not only contribute to a healthier planet but also reflect a movement toward more responsible consumer choices. By being aware of these practices, you can make informed decisions that align with your values of freedom and environmental stewardship.
Frequently Asked Questions
How Long Does Vinyl Plank Flooring Typically Last?
Imagine your floors as a sturdy ship sailing through years of wear and tear. Vinyl plank flooring typically lasts 10 to 20 years, depending on durability factors like foot traffic and maintenance. Your lifetime expectations can be influenced by the quality of the material and installation. To maximize longevity, consider regular cleaning and avoiding excessive moisture. When cared for properly, your vinyl planks can weather life's storms and remain beautiful for years to come.
Can Vinyl Plank Flooring Be Recycled After Use?
Yes, vinyl plank flooring can be recycled after use, though the recycling processes vary. Many facilities can handle it, reducing environmental impact. However, it's essential to check local regulations and available services. By ensuring proper recycling, you contribute to a circular economy, minimizing waste. You've got the power to make a difference by choosing recycling options that align with your values, promoting sustainability while enjoying the benefits of vinyl flooring.
Is Vinyl Plank Flooring Waterproof or Water-Resistant?
Imagine you've just installed vinyl plank flooring in your kitchen, and you're wondering how it'll hold up against spills. Vinyl plank flooring is water-resistant, meaning it can handle minor moisture, making it ideal for areas prone to spills. Its installation methods often include a waterproof backing, enhancing moisture resistance. However, it is crucial to clean up excess water promptly to prevent any long-term damage, especially in high-humidity environments like bathrooms or basements.
How Does Vinyl Plank Flooring Compare to Hardwood Flooring?
When comparing vinyl plank flooring to hardwood, you'll find a significant cost comparison. Vinyl is generally more affordable, making it appealing for budget-conscious homeowners. However, the durability debate looms; while vinyl resists scratches and moisture, hardwood offers timeless elegance and can last decades with proper care. Ultimately, your choice should reflect your lifestyle needs, aesthetic preferences, and long-term investment goals, balancing initial costs against potential maintenance and replacement expenses.
What Maintenance Is Required for Vinyl Plank Flooring?
Maintaining vinyl plank flooring requires regular cleaning methods to keep it looking pristine. You should sweep or vacuum to remove debris and occasionally damp-mop with a manufacturer-recommended cleaner. Surface protection is essential; using mats or rugs at entry points can prevent scratches and wear. Additionally, avoid harsh chemicals that can damage the finish. With consistent care, your vinyl flooring will remain resilient and visually appealing, allowing you to enjoy its benefits without hassle.